Fiberglass Resources
Fiberglass Basin Specifications
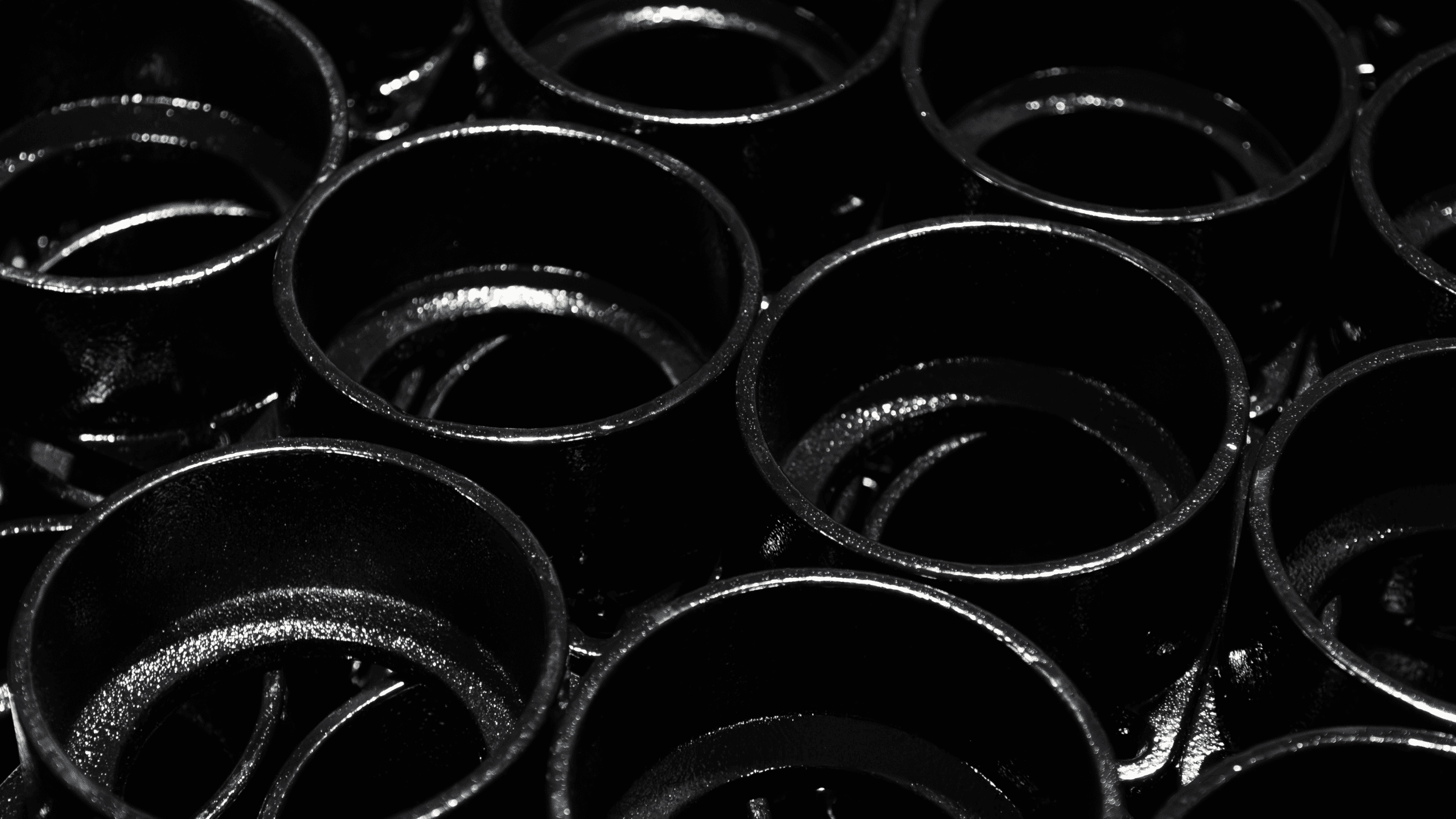
Contact Us Today
Send us a message and someone from the division you selected will get back to you as soon as possible.
Contact Us
Contact Us
Contact Us
GENERAL
Unless otherwise indicated, the plastics terminology used in this standard shall be in accordance with the definitions given in American Society for Testing and Materials (ASTM) Designations D3753-99.
Unless otherwise indicated, the plastics terminology used in this standard shall be in accordance with the definitions given in American Society for Testing and Materials (ASTM) Designations D3753-99.
MATERIALS
Resin – The resin used shall be of commercial grade and shall either be evaluated as a laminate by test or determined by previous service to be acceptable for the environment.
Reinforcing Material – The reinforcing material shall be a commercial grade of glass fiber having a coupling agent which will provide a suitable bond between the glass reinforcement and the resin.
Laminate – The laminate shall consist of an inner surface, an interior layer, and an exterior layer of laminate body.
Inner Surface – The inner surface shall be free of cracks and crazing with a smooth finish. This may be a gelcoat surface or reinforced with glass surface veil.
Interior Layer – A minimum of 0.100 inch of the laminate next to the inner surface shall be reinforced with not less than 20 percent nor more than 30 percent by weight of noncontinuous glass strands having fiber lengths from 0.5 to 2.0 inches.
Exterior Layer – The exterior layer of the body of laminate shall be of construction suitable for the service intended and contain sufficient glass by weight to provide the aggregate strength necessary to meet the tensile and flexural requirements. The exterior surface shall be relatively smooth with no exposed fibers or sharp projections. Handwork finish is acceptable, but enough resin shall be present to prevent fiber show.
TANK WALL
Must be designed to withstand wall collapse based on the assumption that saturated soil exerts hydrostatic pressure of 120 pounds per cu. ft. The tank wall laminate must be constructed to withstand or exceed two times the actual imposed loading on any depth of the basin. Stress calculations must be submitted verifying the results obtained using 120 pounds per cu. ft. hydrostatic pressure and two times actual imposed loading on any depth basin. Depth of bury to be specified on purchase order with wall thickness calculated and guaranteed by AK Industries.
Must be designed to withstand wall collapse based on the assumption that saturated soil exerts hydrostatic pressure of 120 pounds per cu. ft. The tank wall laminate must be constructed to withstand or exceed two times the actual imposed loading on any depth of the basin. Stress calculations must be submitted verifying the results obtained using 120 pounds per cu. ft. hydrostatic pressure and two times actual imposed loading on any depth basin. Depth of bury to be specified on purchase order with wall thickness calculated and guaranteed by AK Industries.
TANK BOTTOM
Must be constructed suitable for the service designated by the project engineer. Under totally water submerged conditions, the center deflection of any empty tank bottom must be less than 3/8 inch as not to interfere with bottom pump mounting requirements and rail systems. AK recommends all basins over 10′ in depth to have a steel insert.
Must be constructed suitable for the service designated by the project engineer. Under totally water submerged conditions, the center deflection of any empty tank bottom must be less than 3/8 inch as not to interfere with bottom pump mounting requirements and rail systems. AK recommends all basins over 10′ in depth to have a steel insert.
APPEARANCE
The finished laminate shall be as free as commercially practicable from visual defects such as foreign inclusions, dry spots, air bubbles, pinholes, dimples, and delaminations.
The finished laminate shall be as free as commercially practicable from visual defects such as foreign inclusions, dry spots, air bubbles, pinholes, dimples, and delaminations.
BASIN
The pump basin shall be constructed of fiberglass in any AK standard diameter up to and including 120″ and specified depth. The bottom of the basin shall be reinforced with a fiberglass plate extending beyond the basin diameter for anchoring to a concrete pad. Pump mounting studs will be attached to this plate and installed in pump basin per your specifications or prints.BASIN INSTALLATION INSTRUCTIONS
The pump basin shall be constructed of fiberglass in any AK standard diameter up to and including 120″ and specified depth. The bottom of the basin shall be reinforced with a fiberglass plate extending beyond the basin diameter for anchoring to a concrete pad. Pump mounting studs will be attached to this plate and installed in pump basin per your specifications or prints.BASIN INSTALLATION INSTRUCTIONS
- Inspect all materials supplied by and/or installed by AK Industries to assure there are no damages due to shipping prior to installation.
- Excavate hole large enough to accommodate basin, underground piping, backfill material, and adequate working space.
- Prepare the bottom of the excavated hole with 6″ of backfill material or concrete pad. Check base to ensure it is level and smooth.
- Install basin on gravel base or concrete pad, anchor if necessary.
- Concrete may be poured around basin bottom if ballast is required for buoyancy.
- Backfill with pea gravel 4″ to 6″ around the entire periphery of the basin. Compact backfill material in 12″ lifts. Stop and connect piping as required.
Recommended Backfill Material
Gravel or stone to be free-flowing, naturally rounded aggregate with a particle size of not less than 3/8″ or larger than 3/4″ in diameter.
Gravel or stone to be free-flowing, naturally rounded aggregate with a particle size of not less than 3/8″ or larger than 3/4″ in diameter.
Caution: If burial depth is greater than the basin height, consult a factory representative to assure structural integrity is not compromised. Reinforcement may be required.
Caution: In freezing conditions, backfill material must be dry and free of ice. Do not use other backfill materials. In areas where the specified materials are not available, contact AK Industries, Inc.
Caution: Warranty is void if other than approved backfill materials are employed without prior written approval from AK Industries, Inc.VALVE BOX INSTALLATION INSTRUCTIONS
- Inspect all materials supplied by and or installed by AK Industries to assure there are no damages due to shipping prior to installation.
- Excavate hole large enough to accommodate basin, underground piping, backfill material, and adequate working space.
- Create a step to support valve vault and prepare the bottom of the excavated hole with 6″ of backfill material or concrete pad. Check base to ensure it is level and smooth.
- Install valve box unit on gravel base or concrete pad, anchor if necessary.
- Concrete may be poured around basin bottom if ballast is required for buoyancy.
- Backfill with pea gravel 4″ to 6″ around the entire periphery of the basin. Compact backfill material in 12″ lifts. Stop and connect piping as required.
Recommended Backfill Material
Gravel or stone to be free flowing, naturally rounded aggregate with a particle size of not less than 3/8″ or larger than 3/4″ in diameter.
Gravel or stone to be free flowing, naturally rounded aggregate with a particle size of not less than 3/8″ or larger than 3/4″ in diameter.
Caution: If burial depth is greater than the basin height, consult a factory representative to assure structural integrity is not compromised. Reinforcement may be required.
Caution: In freezing conditions, backfill material must be dry and free of ice. Do not use other backfill materials. In areas where the specified materials are not available, contact AK Industries, Inc.
Caution: Warranty is void if other than approved backfill materials are employed without prior written approval from AK Industries, Inc.